Membrane Pressing
Northern Contours is one of the most highly qualified & experienced pressers of cabinet doors and surfaces
in North America. Membrane Pressing 3D Laminate (Thermofoil) and Wood Veneer is the technique that put us on the map.
It’s an art that we’ve spent 25 years perfecting, and we’re excited to share our expertise with you.
Thermofoil cabinet doors and surfaces begin with an engineered core that’s 100% recycled, EPA-CPA certified, and CARB II compliant. After cutting and routing the core to desired door styles and profiles, the board goes through a gluing process. Next, components are laminated with 3D Laminate (Thermofoil) material. Through a combination of heat, vacuum, and positive pressure, the material is bonded to the engineered substrate. Membrane pressed cabinet doors and components are left seamless and free of edgbanding because the material is pressed over the component’s face and sides. Both the pressing process and the material itself give our components their durability as well as resistance to wear and water damage.
The membrane pressing process for our Wood Veneer cabinet doors and surfaces has also been perfected to create stunning end products. Again, it starts with 100% recycled, EPA-CPA certified, and CARB II compliant engineered core. After cutting and routing to desired door styles and profiles, cabinet door and surface components are edgebanded, then membrane pressed for a clean, contemporary look.
Northern Contours uses a combination of Wemhöner membrane presses and Shaw membrane presses to produce the highest quality products in the industry. With their deep tray, Shaw presses help us produce thick components in 3D Laminate (Thermofoil) for various contract applications.
With our pressing expertise and state-of-the-art machinery, we’re able to effectively serve a variety of customers with very different needs. From high volume customers to customers in need of proprietary products with specific or complex requirements, we have the capabilities to get your job done.
Thermofoil cabinet doors and surfaces begin with an engineered core that’s 100% recycled, EPA-CPA certified, and CARB II compliant. After cutting and routing the core to desired door styles and profiles, the board goes through a gluing process. Next, components are laminated with 3D Laminate (Thermofoil) material. Through a combination of heat, vacuum, and positive pressure, the material is bonded to the engineered substrate. Membrane pressed cabinet doors and components are left seamless and free of edgbanding because the material is pressed over the component’s face and sides. Both the pressing process and the material itself give our components their durability as well as resistance to wear and water damage.
The membrane pressing process for our Wood Veneer cabinet doors and surfaces has also been perfected to create stunning end products. Again, it starts with 100% recycled, EPA-CPA certified, and CARB II compliant engineered core. After cutting and routing to desired door styles and profiles, cabinet door and surface components are edgebanded, then membrane pressed for a clean, contemporary look.
Northern Contours uses a combination of Wemhöner membrane presses and Shaw membrane presses to produce the highest quality products in the industry. With their deep tray, Shaw presses help us produce thick components in 3D Laminate (Thermofoil) for various contract applications.
With our pressing expertise and state-of-the-art machinery, we’re able to effectively serve a variety of customers with very different needs. From high volume customers to customers in need of proprietary products with specific or complex requirements, we have the capabilities to get your job done.
Solutions
- 3D Laminate Seating Components
- Shelving
- Tablet Arms
- Fixture Components
- Frames & Mullions
- 3D Laminate Cabinet Doors
- Crown Moulding
- Appliance Panels
- Fillers & Rosettes
- Valances
- Wine Racks
- Profiled 3D Laminate Surfaces
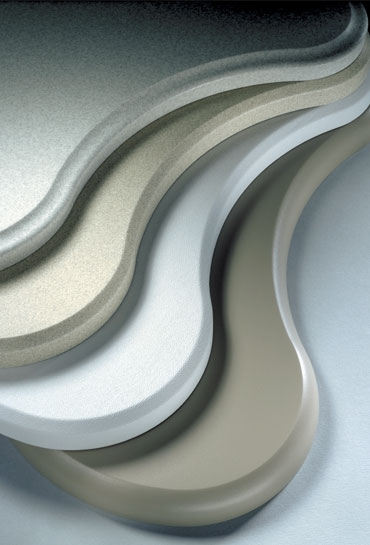
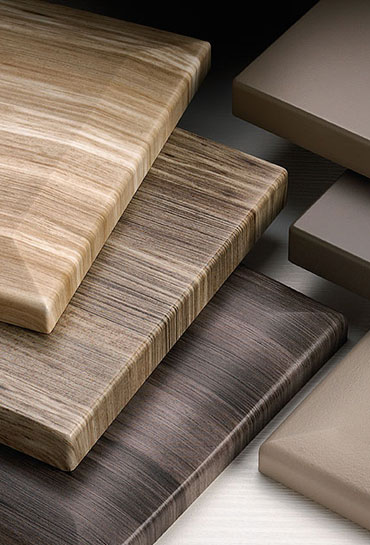